Monday, December 05, 2005
A weekend of ups and downs
The finished product of the survey will be a topographic map of the site with 1-foot contours. Currently, the best topo we have is the USGS 10-foot contours. That only gives a rough idea of the site, not enough detail to plan any building locations, roads or ponds and water catchment locations.
We did not survey the entire site, partly because there is a "tail" section that we aren't likely to "develop" to the extent that a 1-foot topo is needed, and partly because we wanted to take all the "shots" within two days.
The process was very instructive. Modern surveying equipment makes the job way different from when I played surveyor as a kid with a scope and a friend with a marked stick. The primary piece of equipment, the transit or theodolite, is a complex box about the size of a few bricks. It calculates direction, angle of elevation above or below, and, using infrared beams, the distance to the "stick" to within thousandths of a foot.
The "stick" is an extendable pole with a point on the top and bottom with a very precise circular mirror at a fixed height. Markings on the inside pole tell one how far from the ground the point is. These mirrors are remarkable. They are actually made of six mirrors that each are precisely 60 degrees of the circle. These are precisely set in a concave six-sided pyramid so that no matter from which direction one looks into the assembly, one sees the same picture of oneself. Move up or down, left or right, and one still sees the same part of one's face. This is very important, of course, because the mirror needs to precisely bounce the infrared beams back to the transit, and the stick holders cannot possibly get a precise 90 degree angle on the transit from sometimes hundreds of feet away.
So the process is to set up the transit on a point and take "shots" of the sticks at various points within sight of the transit. Each of these sightings are stored in a computer as data points. When all the points that can be shot from the transit are taken, the transit is moved to another point. A stick is placed where the transit was, and a shot is taken from the new point back to the previous point to verify their relationship to one another.
This process continues across the entire site, setting transit points by "backshooting" to earlier ones, and taking shots in every direction from each transit point. The more shots, the more precise the end product will be.
The trick is to take enough shots to get all the contour changes so the computer, where all the data points are processed, can place the data points on the map and interpolate between them to describe the contour lines. To get the best detail one must take shots on the center line, the "center of flow", of each stream, and the "toe" and "top of bank" on both sides. These five shots are taken at points along each stream where the route or the elevation changes. Shots are taken where there are changes in the slope, and also at scattered points across the entire area.
Again, the more shots, the better the product, but, obviously, there's a point beyond which the cost would outweigh the value of the extra precision. With two days to take the data points, we had to decide where to spend more time to get more shots and more detail, and where more detail wouldn't be all that useful, and, consequently, we could take fewer shots and still get what we need.
Within a week we should see the result of our work.
Thursday, November 24, 2005
Working with Ball State
Over the next few days a few phone calls were exchanged and the two classes, one in landscape architecture and one in architecture, worked on their respective assignments.
Finally, on Monday the 21st, a mere seven days after their site visit, the classes presented their plans to us at Ball State.
Unlike the class project last year, this year's group worked their proposals as a group and gave a single group presentation. (Last year each student proposed a complete site plan of their own.) This year's format worked better, I think, because, with only one proposal to create, there was no redundancy in various proposals. Students were able to discuss their ideas as a class, with the class choosing the best of them for inclusion.
Ideas that were especially interesting include:
- adding a large area attached to the barn in which the stairways would be located,
- infilling the barn walls with straw bales with at least one of the walls covered on the outside with transparent panels to show the bales,
- creating sets of water catchment areas to hold rain water on the hillside above the comunity area allowing it to be used for irrigation,
- moving some of the commuity activites to the third floor of the barn; and,
- building a boardwalk across the wetland area to protect it and allow more reliable access regardless of the weather.
Since it is likely that the community building will not be built for at least five years, one issue that was discussed was using the barn for more of the community purposes. This means designing the barn with more thought for larger group meals and perhaps moving a few "barn" things, like equipment storage, to a separate building.
This was all good food for thought.
We hope our relationship with Ball State faculty continues as Raccoon Creek Community grows over the years. Having a nice place for overnight class visits is one reason we are planning for dorm rooms in the barn.
Monday, October 31, 2005
We're half way there
A small but fiesty group of would-be (make that "will-be") permaculturists has completed the first half of the curriculum for permaculture design certification. Starting on October 21st and ending on the 29th we spent 8 days at the retreat center learning many aspects of permaculture. We also visited Raccoon Creek twice.
On the first visit the whole class created a swale on a steep hill on the edge of the property and planted a cherry tree. A swale is a trench that (usually) follows the contour of a hill. Its purpose is to trap water running downhill and hold it while it seeps into the hillside rather than running quickly off the hill and likely taking some top soil with it.
The soil removed from the trench is piled on the downhill side so the trench will hold more of the runoff. Over the next hours or days after a rain fall or as a result of snow melt, the captured water will seep into the ground below the swale. Gravity will cause the water to move under the swale and downhill. Over time, the soil below and downhill from the swale will retain much of the moisture making the hillside much better at supporting vegetation.
The cherry tree was planted on the downhill side of the swale. The swale was dug a bit deeper at the tree to catch a bit more water. We also nearly covered the small tree with brush to protect it from browsers, namely deer.
On our second visit, three of us took a close look at the strip of land next to the power line which is Raccoon Creek Community's west boundary. There is a fifty foot easement on each side of the property line demarked by a barbed wire fence and the power line runs above it.
The assigment: How can the power line easement best be used? Develop a plan for improving the land and making it as productive as it can be.
We walked the length of it and found parts of the hill too steep to use, the wetland area ripe for developing, multiple eroded areas where a well pastured field drains across the easement into our woods, and a serious erosion problem at the creek on the southern end.
The entire plan had to be developed in about 3 hours, including the tour, travel each way, and drawing up the plan. Obviously, more detail would be needed later, but we took to the assignment enthusiastically. Here are our recommendations:
For the hillside: a few more swales and eventually a few terraces on the steepest side, the west. As the swales are dug, trees and companion plants would be placed along and between them. Further, we should make the tree line crenulated, that is, rippled, uneven, winding, so that more edge is created between the mowed and the untouched areas.
For the wetland: creation of chanampas -fingers of gardens protruding into a water body that are raised above the water using the soil removed from the wetland. Each of the "fingers" would have a path through the middle to allow for planting and harvesting. Along the width of the wetland area, their number would determine their width, or vice versa, and whether the path through each would be simple and straight or connect a series of "keyholes" that would enlarge the reachable area on each peninsula.
For the eroded areas: begin to slow the erosion by filling in the young gullies with fallen wood, rocks, whatever is nearby. Over time, water flow from the uphill neighbor's pasture will cause nature to fill in around the debris and make the edge along the trees more smooth. This will slow the runoff and cause it to flow into the woods along a longer edge.
For the creek bank: first, raise a ten foot long area at the base of the hill about three feet to cause the runoff to flow through the woods rather than straight into the creek. Next, plant the existing bank with whatever plants will best hold the remaining soil and absorbe the remaining flow.
Finally, along the entire length of the right-of-way we would define a path for walking and make sure it is built as necessary so it will not cause erosion on its own.
Our instructors added a few suggestions. Most significant of these was to take out a few more trees to create some micro climates along the wood's edge and to add some smaller plants along the tree line, if possible, (need to negotiate with the power company) to soften the edge between the mowed right-of-way and the treeline. The power company has trimmed the trees at almost exactly 50 feet from the center line, from the bottom of the tree all the way to the very top! They did not even make healthy cuts, with branches lopped off at fifty feet regardless of how much branch was left protruding from the tree. We hope we can take responsibility for maintenance of the right-of-way in the future.
These poor cuts should be repaired by cutting all the way back to the trunk of each tree, at least as far up the trees as we can get without the large equipment the power company uses.
(A few pictures coming soon.)
Tuesday, October 04, 2005
Unloading and stacking wood
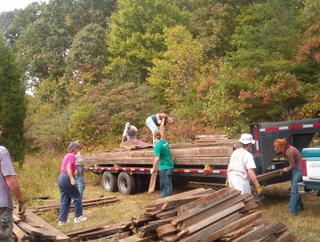
Here are a few pictures from the work day on Sunday. It wasn't a particularly exciting effort, but we had to get the barn parts under cover and protected for the winter.
Five members, two volunteers, three who came with the truck and trailer, and one very small person were on site to help unload the trailer. The truck bed lifts, so it unloaded itself, though we had to stack all the beams that were on it and some from an earlier load more neatly.

A few critters showed up to watch us work. This praying mantis is the first I've seen on the site. It has already turned a bit brown and would have been invisible if it had stayed on the meadow grasses. It was actually larger than it appears here - about six inches long.
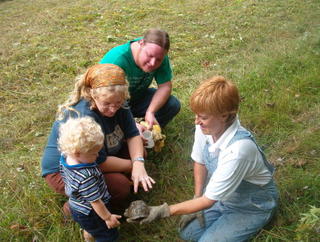
We still could benefit by consolidating some of our wood stacks and moving one or two a bit further from the center of the clearing. Maybe when it cools off a bit. It's not supposed to be in the high 80's in October.
Friday, September 30, 2005
It's all down

It's been a long summer. After nearly 20 working visits to the barn site, and a few trips to Raccoon Creek to prepare for and unload wood from the trucks, it is all down to the ground.
On Tuesday we arrived at the site with a crew of two experienced in taking down barns and an enormous crane that could be raised to about 90 feet and its operator.
The crane was able to lift small and large sections from any part of the barn, all from the same spot. (Remember, the barn was 60 by 54 feet.) It had a "basket" that could lift two men to anywhere on the barn and provided ample space to work without getting in each others' way.
It was interesting to see a few of the crane's

The process was to lift us to a spot, attach a strong strap to one or more barn parts, remove the pins and nails, loosen the part as best we could, then set the basket down to let us out, attach the strap to the crane's hook, and lift the piece or section off the barn and place it on the ground where we could disassemble it.
Sometimes the lift was a single piece, like one of the stringers attaching two posts together longways at the top of the barn.


One mistake we made was not being careful to lay the units down the "right way," meaning with the correct side up to allow us to knock pins out from the top as the sections lay on the ground. We set many of the units down the "wrong way" and lost lots of time later taking them apart.
For each connection, we first tried to pound out the pin and "wiggle" the smaller part's tenon out of the mortise in the larger part. This wiggling wasn't as simple as it sounds. Many of the connections were still very tight after 140 years. We use a long 4X4 to pry and push the beam left and right as someone else inserted a wrecking bar, rock, wedge or board into the crack between the parts. At each change of direction, the crack opened up more and the a larger wedge could be inserted until the beam finally disconnected. It took two people to lift a typical beam, so this wiggling process took some time. Sometimes we were able to pound the pieces apart, but not often.
If knocking out the pin proved impossible, because it was too tight, had bent or broken inside the connection over the years, or the connection was wrong side up, we used a drill to core the pin holding the tenon in the mortise before using the "wiggle method" described above to separate the parts. Often the drill left what can best be described as a wooden straw inside the hole because the drill was just a tiny bit smaller than the pin or because the course of the drill missed part of the pin on the inside. In these cases we had to drill again (and sometimes again) to remove all the pin.
The last resort was to saw off the tenon. We tried to reserve this approach for beams with tenons that had already rotted away and would not be reusable. These beams will be used by attaching them to their posts with strong angular steel plates.
Some of the dismantling on the ground was done on Tuesday and Wednesday by two of us - enough for a truck load of beams. On Friday three of us worked nine hours and another for the last three to take apart every useful post, beam and knee brace. As it was getting too dark to work, the last pieces came apart and we loaded the generator to return it to the rental site.
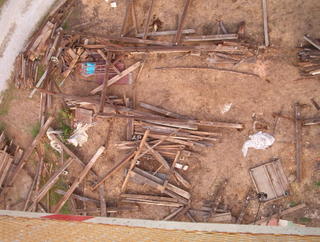
Our selective logging friend was to return on Saturday to load all the useful parts onto his large truck and a long trailer for transport to Raccoon Creek. On Sunday we will meet the trucks and stack all the wood better to protect it for the winter.
I'll post lots of barn pictures on the web site next week.
Wednesday, September 21, 2005
RaccoonCreekForum open discussion list announced
Subscribers are encouraged to discuss issues related to Raccoon Creek, such as intentional community, green building, permaculture, rainwater harvesting, designing for solar power, etc.
Use the input box in the right column to subscribe to the new list named RaccoonCreekForum. Just enter your email address and click on the purple box.
Sunday, September 18, 2005
A fair day
The number of visitors to the fair was down from other years, but the quality of attendees was as high as ever. Many of the participants in the various presentations were as informative as the knowledgeable presenters. There were sessions on homesteading, gardening, herbs, transportation, energy, 32 presentations in all, including a "Chickens in the City" field trip. (I wondered if this was about people afraid to visit the country, but I digress.)
We had a table for Raccoon Creek Community and handed out about a hundred of our new flyers. You can print one for yourself from our web site. Please share it with others.
We met many people who had heard of Raccoon Creek, and many who offered assistance of various sorts. One fellow has been a city planner for many years and offered ideas on working through the various planning stages. One has a landscaping business; at least two have horticulture backgrounds. One woman offered to help us get permission for a larger meeting space for our Bloomington meetings. And we got good advice from timber framers, green builders, and others who wished us well.
Perhaps most encouraging were the people who told me they have been reading this blog. I'll have to check my grammar and spelling better now that I know people are actually reading these posts.
And our new three dimensional map of the site was displayed. Made of cardboard layers cut to match the contour lines on the USGS topographic map for Raccoon Creek, the map was a big hit and made describing the property much easier.
The next meeting is in Bloomington on September 29th. More details will be sent to our "announcements list". If you'd like to be on it, let me know.
Monday, September 12, 2005
Best laid plans
Some of our community went to the barn site on Saturday and moved another large load of wood to Raccoon Creek. The truck owner tagged a few more trees that need to be taken down to allow the larger trailer to get onto the site, so we will spend a day or so between now and the 28th doing a bit more widening.
This weekend we will be manning a table at Bloomington's Simply Living Fair. If you've got an interest in simplifying your life, this fair is a great place to learn how. Visit our table if you can attend, and plan to have dinner with us on Saturday and/or Sunday evening to talk about Raccoon Creek and our upcoming permaculture course. (Discount deadline is the 21st of September.)
The following weekend may be the best time to restack the barn wood that has already been taken to the site. It should be a great time of year to spend a day at Raccoon Creek, or even to camp overnight. Let us know if you'd like to help for a few hours that weekend.
Wednesday, September 07, 2005
Last post before there are no more posts
Last weekend we removed all the nails in all remaining wood that has been taken off the building. All the board were stacked in preparation for transporting them to Raccoon Creek, and a large load of rafters and purlins was moved and slid off the truck in the larger clearing.
Help is needed this weekend to load the truck another time and to stack and cover the wood in the clearing. Loading should take less than a few hours on Saturday, faster with more help. Stacking and covering the load in the field on Sunday will take less than an hour. Please let us know if you can help on either end. I am away until Sunday evening, but you can contact me by email with your phone number and I will pass on your offer to the person coordinating the move.
The next work will begin on Tuesday the 13th when help arrives in the form of a few experienced people and some heavy equipment to allow us to take the beams and posts down. If all goes well the timbers will all be on a large trailer in two days, or maybe three.
Once the trailer pulls away, we'll likely need to return to the barn site for a day to do some final cleanup and remove some trash.
It will be nice to be able to concentrate our energy on the Raccoon Creek site after that. I bet you might be tired of reading about the barn, too.
Sunday, August 28, 2005
The roof is gone!
Using the lift, one person rode to the top of the inside of the barn while another climbed the purlins on the lower pitch of the roof's west side. (The upper pitch purlins were removed weeks ago.) Each pried off one end of each rafter and the "lower" person slide his end aside until it fell off the header and dropped to the ground. This was repeated until all the rafters in a bay were dislodged and dropped.
Then the lift was lowered, moved to the next bay, and raised to the top again. The process was repeated, dropping about 6 rafters for each move of the lift, until the whole west side top pitch was removed.
Then the purlins on the east side top were removed so the rafters could be taken down next. On this side the lift was even more helpful. As each bay of rafters was dislodged at the bottom by the person standing on the lower east side purlins, the lift was used to lift them off the bottom while they were still attached to the top header. This made it a simple task to push the wrecking bar under each rafter, unlike the rafters on the other three pitches, most of which were tightly nailed down and took considerable effort to pry them off. Then, as each rafter was pried off at the top, the lift rider hung onto it while he hung up his wrecking bar, and pushed the rafter down over the hip of the roof and gave it a push. Each rafter slid down the lower pitch and landed on the east side of the barn.
Next the lower east side purlins came off, the bottom four or five rows being removed from the list platform, now on the east outside of the building. Using the lift saved probably 3/4ths of the time for these last rows which otherwise would have had to be removed while standing on a ladder, and climbing down to move the ladder every 6 rafters or so.
On this pitch of rafters, from the lift platform, we pried the lower end up and swung it left or right until it cleared the header it had been nailed to. Then it was dropped just as the top pitch of the west side had been dropped, only not so far.
Finally the lower west side purlins and rafters were removed in the same way as the lower east side.
The bad news: many of the rafters broke when they fell. Many were already cracked, especially at the notches. In some cases the length below the bottom pitch notches - the roof overhang - was already disconnected from the rest of the rafter. Only the purlins, attached to adjacent rafters, had been holding these rafter fragments. Obviously, if the roof is rebuilt like it was, the rafters that are broken or damaged cannot be used.
The good news: All but a handful of the damaged rafters will make great joists for the lofts that had no flooring to begin with.
Next: take out nails, stack and load and transport to Raccoon Creek, take down, load and transport posts, beams and knee braces to Raccoon Creek.
Sunday, August 21, 2005
Barn history
At the time of the 1859 map of Floyd County, the property at what is now 201 Hausfeldt Lane (Hossfeld) was owned by Peter Smeaton and his wife. As of 7-06-05, I have not been able to trace the ownership further back.
On September 24, 1860, the property (66 acres) was sold to Barbara and John G. Beck.
On May 21, 1866, the property was sold to Francis and Louis Fraaz.
On February 27, 1869, Francis H. Fraaz transferred half of the 66 acres to Jacob Vetterlin.
On December 6, 1870, Louis Fraaz and Anastatia, (his wife) and Jacob Vetterlin sold all 66 acres to William Geltmacher.
On November 28, 1872, William Geltmacher and Catherine (his wife) sold the property to Ignatius Ohlmann.
On December 18, 1878, Ignatius Ohlmann (marital status not shown) sold the property to Ernst Hossfeld, my great-grandfather, and the one for whom the road was named.
The farm came down through 4 generations of my family, with parts of the property being sold off at times until there was just under 5 acres remaining, this part containing the barn. This remaining property was sold to the present owner, Janet Burkhart, in September of 2004.
From what I was always told, 3/4 of the barn was existing when my ancestors bought the property in 1875. At that time, the "dog trot" or drive though was down the center of the barn and the barn had a gable roof. According to family lore, my great grandparents enlarged the barn by adding a series of bays to the west side, making the "dog trot" off center, and by splicing 2 sets of upright posts and raising the roof, they made the roof into the gambrel shape as is exists today.
In some publications, I've read, the barn was dated as going back to the 1860's and early 1870's. As there were a number of owners during that time period, it could have been erected by any of a number of persons.
My father ran the farm until the 1960s. After that the farm was sharecropped and the barn no longer used. A lot of the ground was sold in 1980 and the farm ceased operations; thus, the barn was not used except for storage since that time.
If anyone should stumble across any additional information about the barn, please contact us.
Saturday, August 20, 2005
Moving day
Truck rental was an expense I had hoped to keep to a minimum. The going rate for mileage charges for trucks here is $.79/mile! By the time we take it back tomorrow we will have put almost exactly 400 miles on it, and I was so sure we could find a truck to borrow.
We stacked the "good stuff" this morning before heading back to the barn site for another load. Tomorrow we plan to just dump everything off and try to get the truck back before the established return time. I hope we have enough time to cover all the piles with tin roofing. There's plenty of roofing, but I'm not sure there will be plenty of time.
We'll have to get some folks down to the site over the next few weeks to get the lumber sorted and stacked neatly. Otherwise, when we need it in the spring, we'll spend too much time searching for what we need.
Left to do at the barn site:
Remove remaining purlins and rafters.
Take down all posts and beams.
Truck posts and beams to Raccoon Creek
Monday, August 15, 2005
everyday matters
Saturday, August 13, 2005
Permaculture Course details - Web site
Web site
Due to a gift of DSL service for my birthday and the pending loss of my old web site that came with the soon-to-be-defunct email address, I have finally made the effort to set up a simple web site for the Raccoon Creek Community.
Our new web address is http://a.domaindlx.com/RaccoonCreek/.
It's not fancy but it should be an easier way for one to find information about us without having to scrool through "Up the Creek..." and its various monthly archives.
Over time I'll try to expand the web site to include more pictures and specific information. If there is specific information that you'd like to see there, let me know.
Permaculture Course Announcement flyer
For now, the web site's prime purpose is to provide a home for the "Permaculture Course Announcement flyer."
It would be great if you would distribute the announcemnt to anyone who might be interested. Note especially the discount offered for registration by September 21st, a month before the start of the course. Campers can save another $50.
Tuesday, July 26, 2005
65760
"Yeh, so what?" you ask.
Tecumseh happens to be the community closest to East Wind, an intentional community in the Ozarks that was started in 1973 and has 75 residents today.
"And?"
And East Wind is the subject of an article starting on page 114 of the new August 2005 National Geographic magazine.
"OK, so why are you telling us?"
I mention it in an attempt to preempt someone from walking up to me to with a smirk to say, "I saw your 'commune' in National Geographic." Though Raccoon Creek Community will have some property owned in common, it is not a commune, and we will not be shared clothing, nor partners.
See "Eco-village?", "How's your commune coming?", and "A community by any other name - definitions" for a brief explanation of community terms as I understand and use them in this blog.
The article is brief but interesting. The nice folks at East Wind are doing their thing, their community has evolved over 32 years into what they have decided it should be, and it appears to be an interesting place to visit.
The article describes some of the rules and methods they use to manage their community and run their successful nut butter business. I'm sure there are things we can learn from them, and probably some things we can't.
Monday, July 25, 2005
Class fee set for Permaculture course
Remember, this is the first of a two-part program that earns one a Certificate in Permaculture. With that, one may advertise themselves as a Permaculturist. The second 8-day class will be held in the spring.
Soon we will publish details of the course, including directions and a course outline. The instructors will be Peter Bane and Keith Johnson, co-editors of "The Permaculture Activist." Peter and Keith have been the instructors for the Permaculture course that has been taught in the summer for the last few years as an Indiana University elective course. That course is scheduled for two full weeks and a weekend in a row.
This is the Raccoon Creek Community's first major public class. The budget is tight, but if we have a good enrollment, we may be able to afford to reduce the cost of the spring class for those who attend both.
Please tell anyone you think might be interested about the class.
97, 98, 99...
Work has been done on eight days out of the last ten, so we'll soon run out of things that can be done on the ground. None of the roof work can proceed until at least two people who can be on the roof are on site at the same time. Not surprisingly, not everyone wants to get up there.
On Wednesday, an entire loft collapsed while we were removing wood from it, and Mother Nature pitched in by dropping about a third of the north end of the barn in a large storm on Thursday night when we weren't at the site. The same storm lifted a very heavy oak joist that was attached to a tarp for rain and sun protection now that the roof is off, and threw it about 15 feet further into the barn.
The other picture below shows the wood that was brought down "for free."
This coming weekend we'll have another go at it, probably from Friday through Sunday.
Aside from cleaning up little things, there are three major aspects left: finishing the roof - three pitches of purlins and all the rafters; taking down the headers, posts and beams; and moving the disassembled barn to Raccoon Creek.
The roof...
Our hope is to lower each rafter with two ropes managed from the ground as the people on the roof disconnect rafters from each other and tie them onto the ropes.
Before any of this can begin, we need to reinforce, and, in one case, supplement, three of the main posts along the north wall. We had known for some time that some of the posts would need to have their bottom foot to three feet replaced with sound wood when we reconstruct the barn, but the extend of damage to these three main posts was unknown until all the stalls, mangers, and loft floors and joists were removed. I think we can nail some of very solid (and very heavy) oak joists at multiple points to the bottoms of the bad posts to keep them stable while the rafters and remaining purlins are removed above them. This added support can remain on the posts until each is lowered to the ground and stacked for transport.
Major posts and beams...
We have discussed various methods of lowering the posts and beams. Hiring a large crane would be the quickest, but also the most expensive. Since we are trying to save the mortise and tenon connections between posts and beams and knee braces, a crane would be idle more than it was running to allow us time to pound (or drill) out the pins holding the connections. If we sacrific the pinned joints we could cut the connections with a saw and speed the rwmoval.
We discussed renting a cherry picker or a man-lift to get us up to each connection while we knock out the pins and tie the beams for lowering, and then using the same device to help lower them. The problem with this approach is that the beams may be too heavy to be lowered by the device which would also be supporting the weight of the operator.
We are considering starting from a corner and disconnecting each post from the beams connecting it, then lowering it, disconnecting the other end of each beam, and lowering each of them. The process would continue from post to post, always working on an outside corner post. We'll be discussing this approach with our advisor to see if it is feasible. It would take longer, but the cost would be very low, just lots of rope and pullies.
Moving the disassembled barn to Raccoon Creek...
We are trying to develop an inexpensive plan for loading, moving and storing the barn until next spring. That might employ a flat-bed trailer, or a covered trailer. The covered trailer, if kept over the winter would serve the added purpose of storing the lumber, and maybe other things, on the site. A flat-bed, on the other hand would be easier to load but the lumber would need to be covered in some other way.
If you know of anyone who might be able to help with this transportation and storage problem, please let us know at rcc@netdirect.net. If we don't solve it inexpensively, it could become the most costly aspect of the entire project.
Birds
Most of the swallows have now left with only two nests lost with either eggs or babies in them. About a month ago a nest was lost because the joist on which it was built just fell over after the boards on top had been removed. The joist had either never been nailed to the beams or the nails had rusted away. In either case, the nest fell with three or four eggs in it. There was nothing we could do.
Last week, though, we were luckier. Even though I had recovered each active nest we found with boards after removing the floor over them, once the roof was removed, last weekend's rain weakened the last swallows' nest and it fell to the ground. This was probably the first water to touch that spot in 130-plus years.
Fortunately I found the nest soon after it dropped. We had plenty of scrap wood, and enough reuseable nails, so I built a quick and dirty nest box on a post high up under a beam and covered it with another wider board.
I put the remains of the nest on the ledge, mostly mud and feathers, and then put in the four babies, each with its first tiny feathers. It might have helped that I was wearing work gloves, so I never actually touched the babies. Happily, the parents found it and continued to feed them! In fact, about 10 swallows swarmed around the nest for the rest of the day, and occasionally over the next few days I was there. Swallows are very protective and constantly swooping and chirping at us as we work near their nests.
See "The three amigos" picture below.
Yesterday, as I was trying to get a closer picture of them in their makeshift roost, of the remaining three who had not yet flown, two of the babies took to the air for the first time. The first of the four had apparently already flown successfully. That left one, and when we left Sunday after 7 PM, he (or she, how would I know?) was still there, occasionally flapping his wings and trying to get the parents' attention. They had essentially abandoned him, but must have had a change of heart since they were again feeding him when we left. He should be gone before the next trip to the barn.
That leaves just one robins' nest to go. Both of those parents are feeding their four babies, at least that's how many eggs there were as seen from the roof last week. If all goes well, they'll be gone before we remove the purlins over their nest.
A legal decision
Our newest member happens to be an attorney and will be doing the preliminary paperwork for us. We expect the Raccoon Creek Community to be "official" at least by the end of August.
Monday, July 18, 2005
Permaculture instruction comes to Raccoon Creek
For those who haven't heard the term "permaculture" or are unsure of its meaning, here are a few definitions as written by others:
o The design of sustainable human habitats based on the observation of natural systems and uses ecological principles to increase diversity and productivity of local human ecosystems. Permaculture designs incorporate food, energy, and shelter for people and animals while linking the needs and outputs of each element of the system. The result is a dynamic yet stable system that sustains itself. Permaculture designs can be developed for any climate and on any scale, from balconies to entire villages.
o The conscious design and maintenance of agriculturally productive ecosystems which have the diversity, stability, and resilience of natural ecosystems. It is the harmonious integration of landscape and people providing their food, energy, shelter, and other material and non-material needs in a sustainable way.
o According to Bill Mollison, the creator of the Permaculture Design Concept, "Permaculture is the conscious design and maintenance of agriculturally productive ecosystems which have the diversity, stability and resilience of natural ecosystems. It is the harmonious integration of landscape and people providing their food, energy, shelter and material and non-material needs in a sustainable way. Permaculture design is a system of assembling conceptual, material and strategic components in a pattern which functions to benefit life in all it's forms."
The course cost will include lodging, meals and a permaculture manual. More information on the course, including a course outline, the cost, instructor bios and other details will be posted here soon.
Please set these dates aside. If you would like to talk about the course before the next announcement, send an email to rcc@netdirect.net.
Sunday, July 17, 2005
Let it rain
Friday went pretty well. Two of us took off more than half of the west side roofing sheets while the others continued to move boards, pull nails, remove some of the lower nails on the roof from a ladder and pick up lots of wood pieces.
Saturday was another story. It started out pretty well, but then it rained, and rained, and rained. We had been to the site a half-dozen times without even a sprinkle, and the first rain waited until the roof was off to drench us. We were up and down the ladder again and again, removing roof panels, hiding from the rain, removing panels, hiding. Some trips to the roof netted only a panel or two before the next squall came through. (Did I mention it rained a lot?)
A tarp was nailed up to make at least one small space on the barn floor that wasn't being rained on, and folks continued dragging boards under the tarp to remove nails. Metal roofing sheets and newly nail-free boards were dragged to the storage area between the rain showers. Almost all of the straw that was piled in a few of the bays was spread around the barn where the rain and our foot traffic had made a muddy mess.
The afternoon forecast was for more of the same, so those who had not planned to stay overnight cleaned up as best they could and got an early start toward home. There were enough pauses in the rain to allow the last 10 roof panels to be taken down before dark with a bit of time left to remove the final ground floor siding from two of the corners.
Sunday, weather wise, was a repeat of Saturday, with just a bit more time before the heavy rains arrived. The sheetmetal was brought into the barn to be used to cover boards we wanted to save. All the purlins were removed from the top pitch of the west side and they were either tossed on the waste pile or brought in for nail removal depending on their quality. Instead of prying up each nail with a crowbar, it proved to be easy to pop them off with a five foot length of two-by-four.
Our "expert" arrived early Sunday morning to critique our work so far and to offer suggestions for the next steps to be taken. If possible we will take down the rafters by lowering them one at a time. If we can do this it will save hundreds of dollars of crane rental and operator time expense. We'll need a generator to saw through the nails that hold rafters together at the peak of the roof and where the two pitches come together on each side. They are held tightly by four large nails in each coupling, and they are nailed tightly to the headers. It is not possible to pry them apart, especially while standing on top of a roof, clipped onto a climbing rope. With a "saws-all" we should be able to both separate each pair from each other, and separate them from the headers on which they rest.
So... it looks like at least one more full weekend before we're ready for a crane. It was suggested today that we might be able to take the beams and posts down using a "cherry picker" like those used to repare power lines and replace street lights. This would save even more money - it should be cheaper than a crane and not require an operator. We'll check into this possibility this week.
And for those of you following the barn project who would like me to get back to discussing Raccoon Creek, stand by. We hope to have a major announcement as early as tomorrow.
Sunday, July 10, 2005
It's slowly coming down
Since then we have made four more trips to the barn, each less than three full days. Most of the siding is now off the first level. Some has been left near the corners to provide stability for a while longer. About half of the higher levels of siding is off also. Some had to be left in place for now because some of it is holding some bad beams in place.
All of the flooring has been removed and almost all of the joists in the lofts. A few have been left in place in case we need to walk around up there when the frame is being taken down. One of the beams collapsed as I was removing flooring from it. It turns out about 4 feet of it had completely rotted away. The floor just dropped about a foot while I was ripping up the boards. Talk about a fright!
Wednesday we started working on the roof. On the fourth try, I was able to toss a weight over the top of the roof with a string tied to it. Then, after tying my 100-foot climbing rope to the string, it took just a minute to pull it over the top, tie it off, and walk back to the east side of the barn.
We were ready to remove the roof but I found it too steep to climb onto. After an evening to think about it, I devised a way to use our two large aluminum ladders to support a third ladder that reached almost to the second pitch of the roof. The picture below, "the ladder stack," shows what we did. With the two large ladders weighted down and slanted to be flat on the roof, we dragged a third ladder, nailed to a wide board, up onto the ladder jacks. It was easy then to climb the first ladder, clip into the rope with my "figure eight", and climb the wooden one.
From its top, the second pitch was an easy crawl. Once on the top slope I could comfortably walk around, sit down, even occasionally set the crow bar and hammer on the surface without their sliding away. Those were the only tools needed for the roof.
It's possible to walk around on the roof on the steep slope, but without some mechanical advantage, it was not possible for me to walk up the slope. Climbing ascenders might have helped, but I don't own a pair, and it wasn't worth the cost to buy them for a single climb. Once the panels start to come off, the purlins make a great ladder, but one has to get that first sheet off.
The same picture below also shows the purlin grid that underlays the tin sheets. It is easy and safe to climb around on it once exposed, so the work was not particularly dangerous. I used a section of old hose to protect the climbing rope from most of the rubbing back and forth on the tin and the exposed purlins.
Since the sheets were put on from side to side, bottom to top, they must be taken off in the reverse order. It is possible to remove one from below another, but it means prying up a corner of the higher sheet to get to the nails that it covers in the lower ones. And even then one must hold up the covering sheet high enough to allow prying the nails underneath. It's not worth it.
On the steeper slope, since it is difficult to slide across the lower sheets as one could do on the top slope to reach the far line of nails, it was easier, despite having to lift a corner on two rows, to take off each "column" of sheeting from top to bottom. Also, the temperature was above 90 degrees. I don't want to guess what the roof temperature was in the full sun in mid-afternoon.
The good news is that in less than two full days, one person, gaining experience as he went, was able to remove a full half of the roof. Next trip the other half comes down. After that, the purlins will be taken off, and, while up there, I'll disconnect the top of the highest siding.
Stay tuned.
Wednesday, June 22, 2005
It's gonna be hot!
Next we'll remove the flooring from most of the loft area, leaving just enough planks to support ladders to reach the highest siding on the inside of the barn ends. We'll remove the nails from all reusable boards as we have so far, even the planks that we keep to support ladders to make removing them later easier and faster.
When the stalls are all apart, the old bins dismantled, and the loft floors taken down, if there's still time we'll start on the siding.
Siding should be removed starting from the middles of each wall since, especially important in old barns, siding provides some rigidity to the structure. Siding near the corners will come off last.
On Sunday we have an appointment to discuss where the barn should be located when it is moved to Raccoon Creek, so we'll have to leave the barn site on Sunday morning. By then we should be just a weekend away from starting to take down the metal roof panels and the purlins - the boards just under the roof sheets. This is the last step before the structure comes down.
If you'd like to help with the work this weekend or later, let us know. Even simple tasks like pulling nails would be a great help, freeing up others to climb the ladders.
Also, if you know someone who could loan a truck for a day or a weekend, we'd love to talk to them.
Monday, May 30, 2005
How I spent my holiday
We also pulled nails and stacked lumber that we might be able to reuse, and sorted the unusable lumber into nail-free and with-nails piles. Maybe we can find someone who could use the wood for campfires or some other purpose. Otherwise it will all likely be burned without fanfare.
The barn still has thousands of feet of Virginia creeper, despite our having removed three times as much last weekend. When the only wood floor on the first floor of the barn was mostly removed today (see extreme lower left corner of "Most bays now empty" below), Virginia creeper was found still alive under the boards. It's nasty stuff to get rid of, but it looks nice on the side of the barn when it's alive.
The entire floor of the first bay couldn't be removed because there are posts on top of some of it. These should not be structural, but there is a post and a beam that may not be reusable due to dry rot, so we left some of the secondary beams in place just in case. In the same picture, the second post shows about two feet of dry rot at the bottom and the one to its left is literally hanging from the beam.
On the next trip to the barn site we'll finish the last three interior walls, knock two large containers apart, remove some large pieces of plate glass, and start removing siding and maybe start on the roof. The barn has five neat old lightening rods, but, alas, they have been reserved by the owner. After that we'll be ready to hire the crane to take down the big stuff.
Over the next few weeks the barn owner-donor will have the barn valued for her charitable gift, and will prepare a "Waiver of Liability" form to be signed by everyone who volunteers at the site for us. The appraisal may not be done for a few weeks, so the timing for our next work day should be just about right.
We think we have access to enough "extra" posts and beams from a few other barns we've been offered to replace any rotted ones we have found. This likely will be done by cutting off the bad part, always at the bottom of the posts where they have been subjected to some standing water over the years, and putting the better post below the cuts. These will be "scabbed on," meaning we will bolt on two or more long wooden strips that will tie the two parts together, or possibly just use some iron straps that will do even better without the added thinkness of the extra boards.
It's getting late, and there's much to do before our vacation starts, so I'll stop now and post this entry. If you have questions or comments about the barn, send me a note.
Saturday, May 28, 2005
A few weeks off
Tuesday, May 24, 2005
One weekend down...
So far we have removed a few dozen old house doors, about 40 old windows, dozens of steel panels that we think may have been from the facade of an old gas station (visible in the right foreground below), a cast iron bath tub (also below), doors from some public restrooms, an old overhead garage door set, quilting frames, over 25 large metal shelving units, dozens of wheeled platforms (original use unknown), various pulleys, hinges, and barn parts, plenty of boards of various sizes, thicknesses, and quality, and enough hay to cover the floor of the entire barn about a foot deep.
The organ (see "Do you need an organ?", May 19th) was taken apart for the wooden panels on the outside by friends of the property owner, and, sadly, the rest of the organ's "innards" were burned to get rid of them. We also helped the owner dispose of a huge pile of tree branches that burned for 44 hours and was still burning when we left the property about 4pm on Sunday.
New Albany is on Eastern Daylight Savings Time but we were on Eastern Standard Time. That didn't make much difference to us except when one of us asked the time of one of the family members.
We still have a lot of things that can come out of the barn before we begin to remove the siding and the roof. There are a few parts of the lofts that are too badly rotted to be used. They will be burned on site or removed for firewood.
There are lightening rods on the roof, but they will be kept by the owner. Other farm items, like a tiller, rain barrels and some hand tools are being kept by the owner also. Metal items with scrap value as seen in the picture are being sold. We still have to dispose of all the old doors and the steel shelving.
We hope to work a bit more this coming weekend, and then we'll step back for a week or two while the owner finishes the steps to assign a value to the barn for tax purposes. We have found smaller barns for sale and will provide some pricing data to help determine a fair market value.
Let us know if you'd like to help. It's real work, but it's been fun too.
Thursday, May 19, 2005
Do you need an organ?
We are obligated to remove everything in the barn so it will be sent to the dump after June 22nd if someone hasn't asked for it by then.
Thursday, May 12, 2005
Nature-deficit disorder
By creating Raccoon Creek Community I dearly hope to encourage our grandchildren, and lots of other children, to visit and learn where food comes from, that spiders are OK, that the woods are not to be feared, that every person and creature has a place and a right to it, that things that do not plug in can be fun too, that there are still places to just be a kid.
Wednesday, May 11, 2005
Unexpected Sunday visitor
See the entry for the black rat snake on the Center for Reptile and Amphibian Conservation and Management's web site. It is also called cow snake, chicken snake, timber snake, black snake, and black climber. This last name makes a lot of sense since we found the snake lazily lying on a warm card table we had been using for our meetings.
By the time I got his picture he had been spooked from the table and was moving away from us. I couldn't believe he had gotten up to the table. He had to climb either a smooth metal table leg or, more likely, the shorter leg of a camp chair and from there up to the table. A good picture of the black rat snake's climbing ability was found on another web site.
Tuesday, May 10, 2005
Where do we go?
Earlier in the week we stopped at a local saw mill for a trash barrel full of sawdust, an easily found, and usually free, local by-product in our hardwood forest area. A scoop for the sawdust was made from a plastic milk bottle with its bottom cut off.
A seat was made from an old wooden chair with its padded seat removed. A five-gallon bucket, like paint or drywall joint compound comes in, was placed under the opening with an initial scoop of sawdust covering the bottom. The seat was set on a piece of plywood leveled with a few small logs. A roll of paper on a stick completed the setup. All of that was wrapped in, and covered by, a tarp strung inside four trees.
There were signs to the facility ("His" and "Hers", though there was only one seat) and a stretch of rope leading from the road to help find it after dark.
Users were told to cover their "contributions" with just enough sawdust to hide them, and we were ready to go -- no pun intended.
Funny, no one volunteered to dispose of the bucket contents when we left, so yours truly took the job. In fact, the task was not as disgusting as it sounds. The bucket contents were thoroughly covered by and mixed in with the sawdust and there was still no odor. After dumping the contents on the compost pile, the bucket was rinsed with water and the water poured on the pile. Then it was covered with more sawdust. (Straw or grass would be better, but none was available. We'll have some next time.) A scoop of sawdust in the bucket makes it ready for the next visit.
Everyone agreed the system worked very well, but we also agreed we should build a more substantial structure to house it until permanent buildings are constructed. A tarp might not be all that pleasant if it were pouring rain. We will plan a work day at Raccoon Creek for June 25th. Maybe we can construct something then.
What a weekend
At least 25 people came by over the weekend. Some just dropped in for a while. Others camped overnight. (See "Tent city" picture.) Folks roamed the trails while community members held a few meetings, and we led three organized hikes, though I use the term "organized" loosely.
Some joined us for meals made by our members while others made or brought their own. Saturday lunch was an assortment of the makings for turkey roll-ups, salad and fruit. Dinner was a great chili, with corn muffins and assorted drinks and desserts.
A world-class fire pit was dug and ringed with rocks and we had a great evening around it on Saturday night. (See "Campfire" picture.) One visitor was our barn "consultant" who spoke to the assembly and answered questions for nearly an hour. He talked about the process of dismantling barns and the choices we need to make as we move forward.
The coals left from the campfire were used to start a fire for breakfast -- oatmeal with lots of things to add. I liked the dried cherries best. Cathy Moore joined us for breakfast and talked about her home and other projects she has built. (See her link in the "Sunday school" entry below.)
Another hike in the morning and a brief meeting for our resident members and it was lunchtime again. Then everyone took down their tents, packed up, and headed home.
We agreed that we should have another open-field later in the summer or fall. I'll announce it here.
Saturday, April 30, 2005
Sunday school at Raccoon Creek
If you can't wait 'til then, or if you can't be at Raccoon Creek on the 8th, check out Cathy's web site.
Friday, April 29, 2005
Spring flowers at last
The power company has cleared their right-of-way on our western boundary, so there's not much to see in that 50-foot swath, but everywhere else the flowers are having their day. I've included a few pictures. If you let us know by May 4th you can join us on the 6th, 7th and/or 8th to see them for yourself and to visit with us to learn more about our plans.
Permaculture at Raccoon Creek
The programs were produced by Bill Mollison in 1991, but they are timeless. Bill is one of two Aussies who coined the term "permaculture" and first wrote about it in detail.
Each program emphasized a different habitat --desert, tropics, cold climates-- and was, understandably, different in many respects from the others. But the similarities are more obvious.
Mollison showed us implementations of permaculture practices in every corner of the world other than the polar areas. One thing that struck me was how wonderful it would be to actually teach someone permaculture principles and see them create a heathy, sustainable life for themselves where previously one seemed unlikely. Perhaps someday Raccoon Creek Community members will be qualified to travel and teach permaculture to people around the world.
But back to the present...
At the start of this summer, for the third year, a permaculture course will be taught at Lazy Black Bear near Paoli, Indiana, as an elective credit class at IU. The course will be squeezed into two full weeks plus a weekend and successful participants will earn permaculture certifications. The class is full, in fact "way" full, with over 40 students!
We have discussed sending some of our members to a permaculture course, but have decided that bringing a course to us would be preferable for numerous reasons. We would be spending class time talking about our site rather than someone esle's. We would be able to train more Raccoon Creek folks for less expense, giving us more trained people to talk through site design decisions. And, by opening the classes to others, we would enable more folks from Indiana and nearby states to be trained on property more like their own. Being trained in Califoria, Oregon, Arizona, or even North Carolina cannot give as much hands-on experience for midwestern climates as can training in Indiana.
So stay tuned right here to keep informed about our progress in scheduling classes. Current thinking would be to schedule the permaculture certification in two parts: "fundamentals" later this summer or fall, and the "design practicum" about this time next spring, close to the end of spring semesters at state colleges.
If you are interested in participating, send me a note so we can keep you posted on our progress in scheduling a course.
Wednesday, April 20, 2005
Now what!?
We are planning the process of taking it down. We'll do what we can ourselves, but if the superstructure is too difficult or dangerous to take down, we'll hire someone with experience to do it.
We plan to go to the site many times and stay at least a few days each time. It will take a few days just to clean everything out of the barn and a few more to remove all the loft flooring and the joists in the lofts.
Then the real fun begins. We'll start by taking off the metal roof sheets. Each is about 24" X 6'. If we're lucky, we'll be able to punch them off from the inside with long poles. As they slide off, we'll remove the nails and stack them. Those that are relatively undamaged can be used at Raccoon Creek for shed roofs, remote parking areas, and maybe for raised planting beds, though we may learn that using them for that is a bad idea. At the same time, as they become completely uncovered, the purlins - the boards nailed to the rafters to which the roofing is nailed - are taken off, "denailed", and stacked. Chances are they will not be reuseable, but we'll try to find a way. Maybe they can be used for deer fences.
Next, or simultaneously if we have more people at the same time, we can start removing the siding. We're told this should be done from the middle of each wall toward the sides since even the siding provides some stability to the barn as it is being taken down. We will continue to remove nails from everything as we go. Though tedious, removing nails is work even youngsters can help with after we move the detached parts safely away from the building.
When all this work is complete it's time to bring in some large equipment, probably a crane, to take off the beams at the top and begin taking down each bent and attached lengthwise beams. As they come down, they will be taken apart and stacked. I forgot to mention that long before any wood comes off the building, each piece is tagged with a code to allow us to reassemble it properly.
That's the main steps. Finally, we'll load it all on a flatbed truck and head toward Owen County. Hopefully by the time we ship the barn we'll know where it's to be rebuilt and we can unload it close to the site and not have to move it again.
Moving this historic barn is a large project and will take many weeks of part-time effort. Help from anyone will be greatly appreciated.
Come on down
We first need to prepare enough spots for tents and maybe set up a composting toilet to use through the summer so we need to know you plan to come. Next year I hope we'll do this a few weeks earlier so we don't miss the earliest wildflowers.
If you'd like to join us for part of a day or the whole weekend, respond to rcc@netdirect.net raccooncreek@gmail.com by Wednesday, May 4th. If you'd like to share the meals we'll be preparing, we need to hear from you by Sunday, the 1st. The cost for the "meal package" - two meals on Saturday and breakfast on Sunday - is $15.00.
You may arrive as early as Friday about 6pm and stay as late as Sunday about 6pm. You must bring everything you need, like dishware and utensils, a tent, camp chairs if you want them, lanterns and flashlights, and food for other than the three meals being prepared. If you have camp tables, tarps, and other camping gear that could be shared, bring that too.
If I hear from you by the deadline, I'll send a detailed list of things to remember and a map to get you there. If you respond later, there's a good chance no one will see your message until after the weekend.
This should be a great opportunity to meet with Raccoon Creek Community members as we will schedule lots of open time for socializing. Kids are welcome. Except for toddlers whom you'll have to keep an eye on, kids can just be "cut loose" between meals to play and explore. Bring cameras and help us catalog the wildflowers, ferns and fungi.
Friday, April 15, 2005
Where we've been
At the end of the spring recess week, two of us attended a program put on by the Historic Landmarks Foundation of Indiana called Barn Again. We thought it would be useful to know more about old barns, and this program is designed to encourage folks to restore and rehabilitate barns rather than allow them to deteriorate. It was held this year in Corydon at a neat old school house that was part of the Underground Railway.
In addition to the presentation which covered nomenclature of barn parts, and good information on repairing damage, we toured four old barns in the Corydon area. Some have already been rehabilitated. Some need a lot of work. The most interesting thing we saw, though, was not a barn but a spring house, two stories tall, with about a fifty-gallon-per-minute spring flowing into it straight out of a rock wall just about 15 feet away. What a great old building!
At the end of the tour we visited a constructed wetland at a mobile home park not too far north of Corydon. It was helpful to see it, and we might incorporate a constructed wetland into our waste treatment plans.
By far the most significant activity of the day was a visit to a barn that was built before 1875. See a few pictures below. The owner of the barn wanted to find someone who would save it by removing it from her property and reassembling it somewhere else. That would be us.
The barn is very large, in great shape, and has many possibiities. Certainly our hope for a barn that would accommodate a few apartments has been met. In fact, this barn is so large we haven't even begun to consider all the simultaneous uses we may find for it. Some of us are going to visit it again this Sunday, measure it, and maybe start cleaning up the inside.
A fellow was recommended to us who might advise us in dismantling, moving and reconstructing the barn. He thinks he can get us the wooden floor of an old roller skating rink that has been in storage. The barn has no floor now, so the rink floor would be a nice feature and would allow us to build the best darn barn dancing site in Indiana.
We'll be scheduling some work days to take down the parts of the barn we can handle ourselves. If you'd like to see it and maybe help, let us know.